When it comes to precision engineering and machining, understanding tap drill diameters is crucial for creating accurate and secure threads. In this comprehensive guide, we will delve into the world of tap drill diameters, exploring their significance, calculation methods, and practical applications. Whether you're a seasoned engineer or a beginner, this article will provide you with valuable insights to enhance your understanding of this essential aspect of threading.
Understanding Tap Drill Diameters
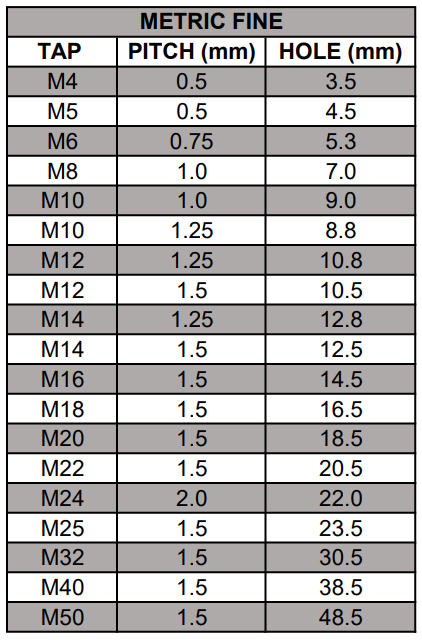
Tap drill diameters play a vital role in the process of creating threads in materials such as metal, plastic, or wood. These diameters determine the size of the hole that needs to be drilled before inserting a tap to cut internal threads. Accurate tap drill diameters ensure a proper fit between the tap and the drilled hole, resulting in strong and reliable threads.
Factors Influencing Tap Drill Diameters

Several factors come into play when determining the appropriate tap drill diameter for a specific application. These factors include the material being threaded, the desired thread size, and the tap style. Different materials have varying properties, such as hardness and ductility, which can affect the drill diameter required.
Material Considerations

- Softer materials like aluminum and brass may require larger tap drill diameters to accommodate the thread form.
- Harder materials such as steel or stainless steel might need smaller tap drill diameters to ensure a tight fit.
Thread Size and Style
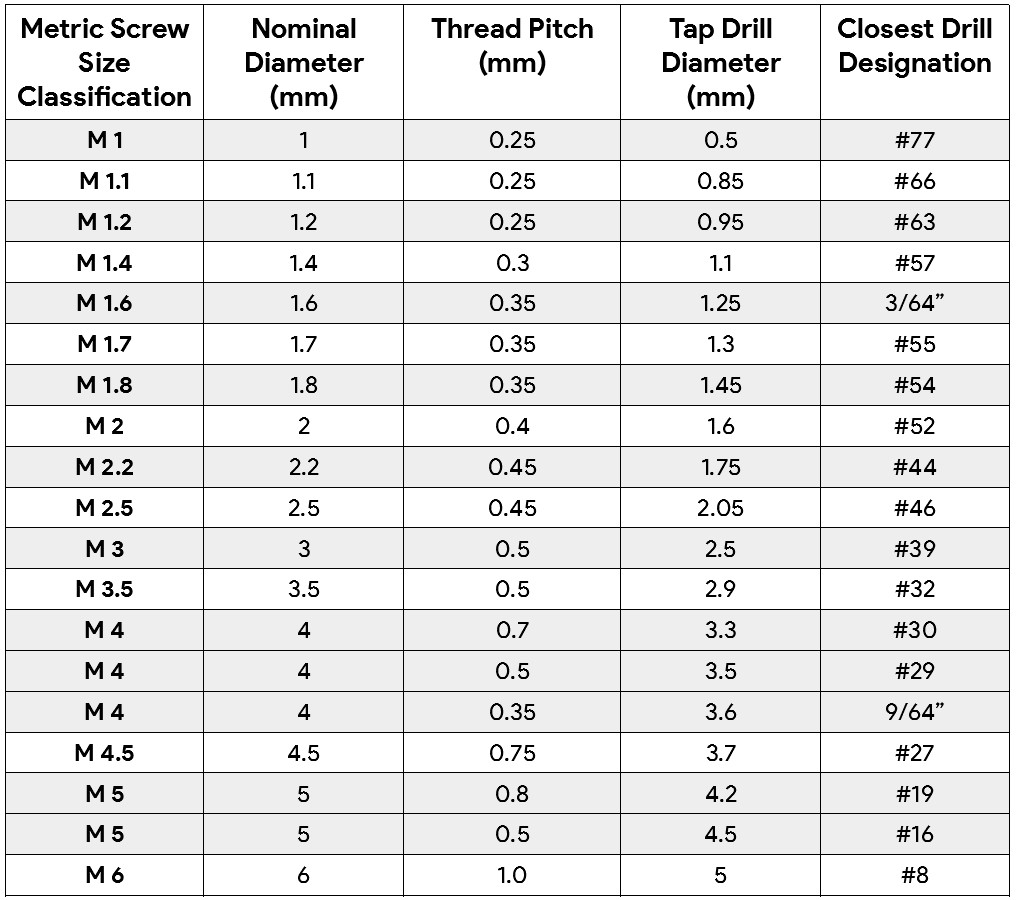
The size and style of the desired thread also influence the tap drill diameter. Common thread standards include Unified Thread Standard (UTS) and Metric Thread Standard. Each standard has specific requirements for tap drill diameters based on the thread size and pitch.
Calculating Tap Drill Diameters

Calculating the correct tap drill diameter involves considering the thread size, thread pitch, and the tap drill point size. Here's a step-by-step guide to help you determine the tap drill diameter for your specific application:
Step 1: Determine Thread Size and Pitch

Identify the thread size and pitch of the desired thread. Thread size refers to the diameter of the thread, while pitch represents the distance between two adjacent thread crests. You can find this information on thread charts or by measuring the existing threads.
Step 2: Choose the Appropriate Tap

Select the tap that corresponds to the thread size and pitch. Taps are available in various styles, including hand taps, machine taps, and spiral point taps. Choose the tap that best suits your application and material.
Step 3: Calculate Tap Drill Diameter
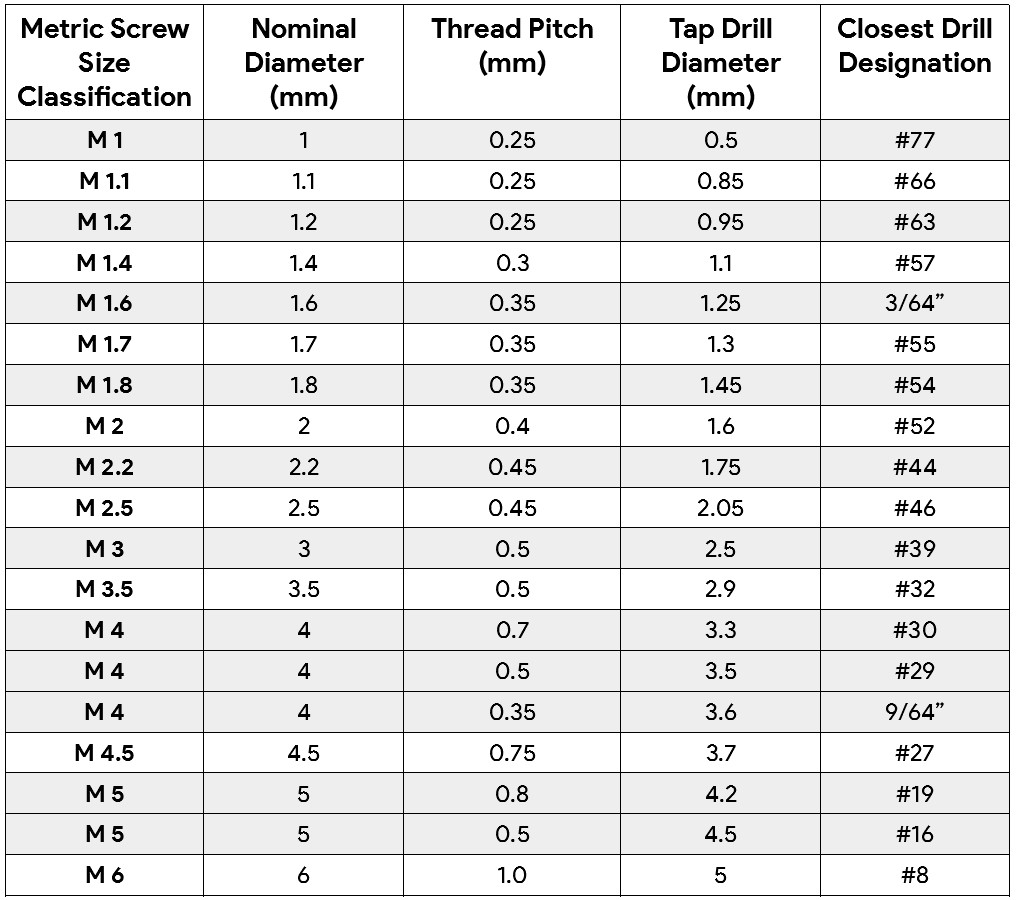
The tap drill diameter can be calculated using the following formula:
Tap Drill Diameter = Thread Diameter - (Tap Drill Point Size x Thread Pitch)
You can find the tap drill point size in the tap's technical specifications or refer to tap drill charts provided by manufacturers.
Common Tap Drill Diameters

While tap drill diameters vary based on thread size and material, here are some common tap drill diameters for reference:
Thread Size | Tap Drill Diameter (inches) |
---|---|
1/4-20 | 0.242 |
5/16-18 | 0.340 |
3/8-16 | 0.410 |
7/16-14 | 0.500 |
1/2-13 | 0.570 |
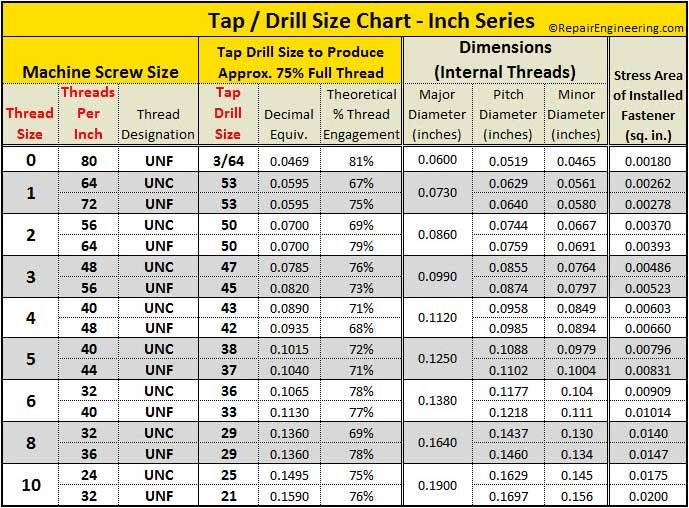
Practical Applications

Tap drill diameters find extensive use in various industries and applications. Here are some common scenarios where accurate tap drill diameters are crucial:
Automotive Industry

- Engine components, such as cylinder heads and valve covers, require precise tap drill diameters to ensure a leak-proof seal.
- Suspension systems and brake assemblies also rely on accurate tap drill diameters for secure connections.
Aerospace Engineering

- Aircraft structural components, including wings and fuselages, demand high precision in tap drill diameters to maintain structural integrity.
- Fuel systems and hydraulic lines also utilize precise tap drill diameters to prevent leaks and ensure reliable performance.
Construction and Manufacturing

- Building structures, such as bridges and skyscrapers, rely on strong and secure connections, making accurate tap drill diameters essential.
- Manufacturing processes often involve threading components, from bolts and screws to hydraulic cylinders, where precise tap drill diameters are critical.
Tips for Successful Threading

To achieve successful threading, consider the following tips:
- Ensure the drilling equipment is properly calibrated and maintained to achieve accurate tap drill diameters.
- Use high-quality taps and drill bits to minimize the risk of breakage or thread damage.
- Choose the appropriate tap drill diameter based on the material and thread size to avoid stripping or cross-threading.
- Lubricate the tap and drilled hole with the recommended cutting fluid to enhance chip evacuation and reduce friction.
Conclusion
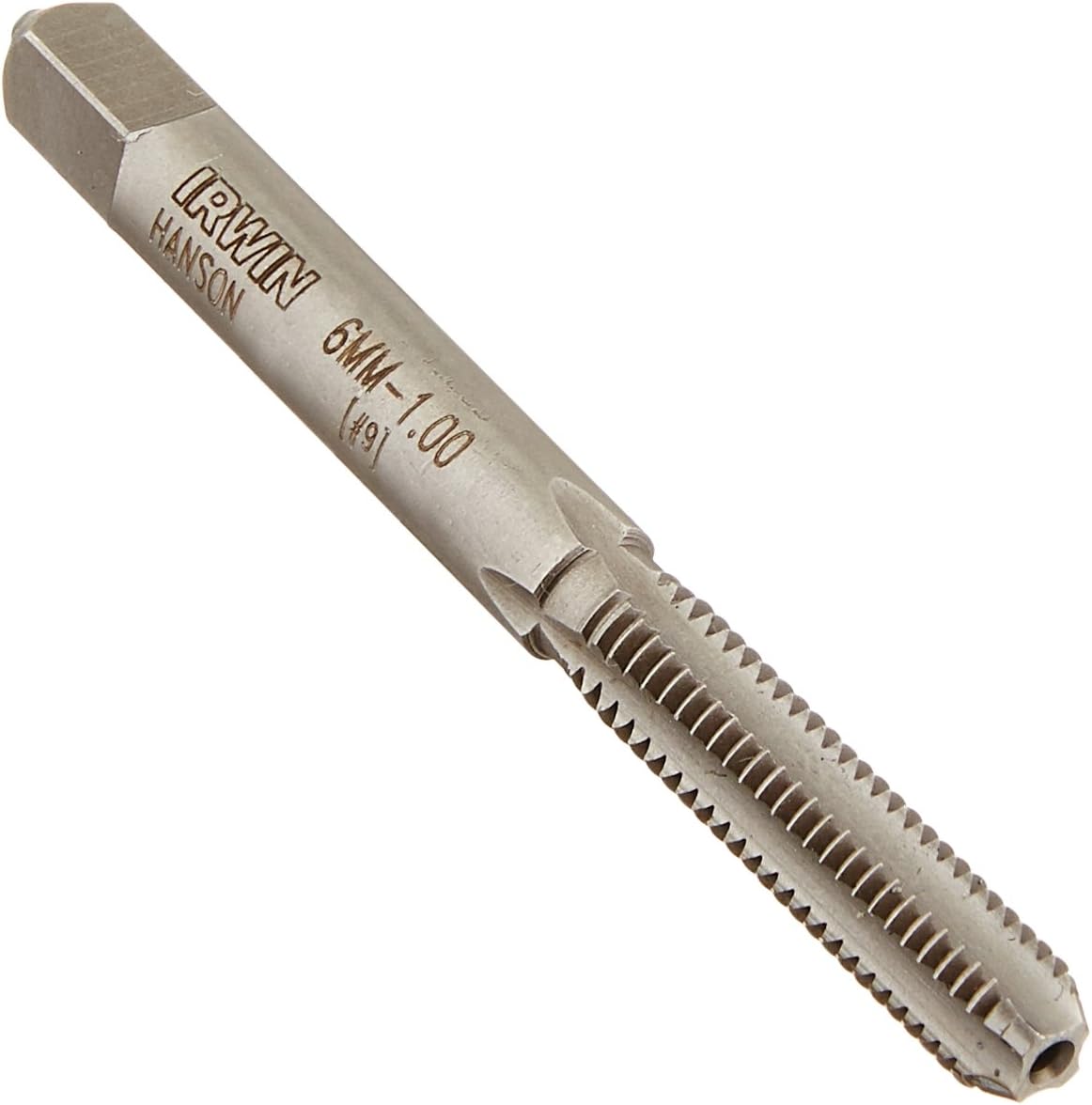
Understanding tap drill diameters is fundamental to creating secure and reliable threads in various materials. By considering factors such as material properties, thread size, and tap style, you can calculate the appropriate tap drill diameter for your specific application. Accurate tap drill diameters ensure a proper fit between the tap and the drilled hole, resulting in strong and durable threads. Whether you're working in the automotive, aerospace, or construction industry, mastering the art of tap drill diameters is crucial for achieving high-quality and precise threading.
FAQ

What is the purpose of tap drill diameters?

+
Tap drill diameters determine the size of the hole that needs to be drilled before inserting a tap to cut internal threads. Accurate tap drill diameters ensure a proper fit between the tap and the drilled hole, resulting in strong and reliable threads.
How do I choose the right tap drill diameter for my application?

+
Consider the material being threaded, the desired thread size, and the tap style. Use the provided formula to calculate the tap drill diameter based on the thread diameter, thread pitch, and tap drill point size.
Can I use a larger tap drill diameter than recommended?
+Using a larger tap drill diameter than recommended can lead to stripped threads or reduced thread strength. It’s crucial to follow the recommended tap drill diameter for your specific application to ensure optimal performance.
What if I don’t have access to a tap drill chart or technical specifications for my tap?
+In such cases, you can consult with the tap manufacturer or seek guidance from experienced engineers or machinists. They can provide you with the necessary information to determine the appropriate tap drill diameter.