Efpi Sensor Bonding is a critical process in the manufacturing and calibration of sensors, especially in the field of electronics and measurement technology. This method ensures the secure attachment of various components, such as fibers, prisms, and mirrors, to the sensor, enhancing its performance and accuracy. In this blog post, we will delve into the intricacies of Efpi Sensor Bonding, exploring its significance, techniques, and best practices to achieve optimal results.
Understanding Efpi Sensor Bonding

Efpi Sensor Bonding is a specialized technique used to join different parts of a sensor system, ensuring their stability and alignment. It involves the use of adhesives, often in the form of epoxy or UV-curing resins, to securely bond the components together. This process is essential for maintaining the integrity of the sensor and ensuring its ability to provide accurate measurements.
The choice of adhesive and bonding technique depends on various factors, including the type of sensor, its intended application, and the environmental conditions it will be exposed to. Let's explore the key aspects of Efpi Sensor Bonding in more detail.
Importance of Sensor Bonding

Sensor bonding plays a crucial role in the overall performance and reliability of measurement devices. Here are some key reasons why proper sensor bonding is essential:
- Accuracy and Precision: Secure bonding ensures that the sensor components remain in their intended positions, minimizing any movement or misalignment that could affect measurement accuracy.
- Stability: Well-bonded sensors are less susceptible to vibrations and external forces, maintaining their stability even in dynamic environments.
- Longevity: Proper bonding techniques can extend the lifespan of sensors by preventing component failure due to movement or exposure to harsh conditions.
- Reduced Calibration Needs: Sensors with reliable bonding often require less frequent calibration, saving time and resources for manufacturers and users.
Techniques and Considerations

The choice of bonding technique depends on several factors, including the type of sensor, its components, and the desired outcome. Here are some common techniques used in Efpi Sensor Bonding:
Epoxy Bonding

Epoxy adhesives are known for their excellent bonding strength and durability. They are often used for sensors that require long-term stability and resistance to harsh environments. The process involves mixing and applying the epoxy to the sensor components, ensuring proper curing time and conditions.
UV-Curing Resins

UV-curing resins offer a faster bonding process compared to epoxies, making them suitable for sensors with tight production schedules. These resins cure rapidly when exposed to ultraviolet light, allowing for efficient bonding without compromising strength.
Anaerobic Adhesives

Anaerobic adhesives, also known as threadlockers, are often used for bonding metal components. They provide excellent sealing and prevent corrosion, making them ideal for sensors with metal-to-metal connections.
Thermal Bonding
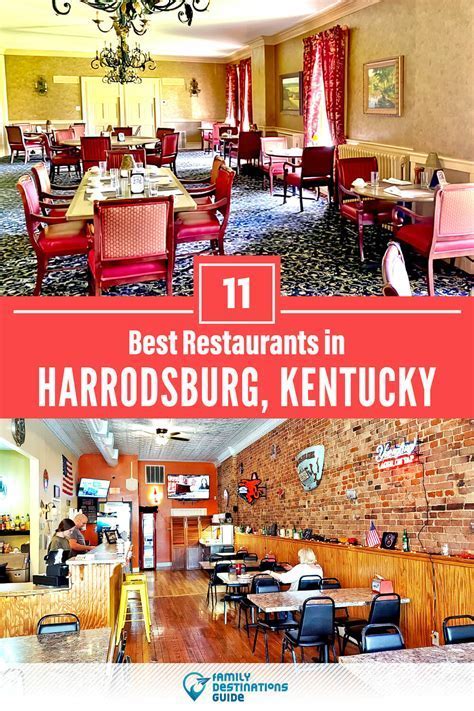
Thermal bonding involves the use of heat to melt and fuse sensor components together. This technique is commonly used for plastic or thermoplastic sensors, offering a strong and permanent bond.
Best Practices for Efpi Sensor Bonding

To achieve optimal results in Efpi Sensor Bonding, it is essential to follow best practices and considerations. Here are some key points to keep in mind:
- Surface Preparation: Ensure that the surfaces to be bonded are clean, dry, and free from contaminants. Proper surface preparation enhances adhesive bonding and prevents potential issues.
- Adhesive Selection: Choose the right adhesive based on the sensor's requirements, considering factors such as strength, cure time, and environmental resistance.
- Mixing and Application: Follow the manufacturer's instructions for mixing and applying the adhesive. Proper mixing and application techniques ensure consistent bonding and avoid adhesive failures.
- Curing Conditions: Adhere to the recommended curing conditions, including temperature and humidity, to ensure the adhesive reaches its full strength.
- Alignment and Clamping: During the bonding process, maintain proper alignment of the sensor components and use appropriate clamping techniques to prevent movement or misalignment.
- Quality Control: Implement rigorous quality control measures to detect any bonding defects or issues. Regular inspections and testing can help identify and rectify problems early on.
Challenges and Solutions

Efpi Sensor Bonding can present certain challenges, especially when dealing with complex sensor designs or specific environmental conditions. Here are some common challenges and potential solutions:
Bonding to Sensitive Components

Some sensor components, such as delicate fibers or fragile mirrors, may be sensitive to certain adhesives or bonding techniques. In such cases, it is essential to choose adhesives with low viscosity or use techniques like capillary bonding, which minimizes direct contact with the sensitive component.
Bonding in Harsh Environments

Sensors used in harsh environments, such as high temperatures or corrosive conditions, require adhesives that can withstand these challenges. Specialized adhesives with enhanced resistance to temperature, humidity, or chemicals can be employed to ensure reliable bonding.
Precision Alignment

Achieving precise alignment of sensor components is crucial for accurate measurements. Advanced bonding techniques, such as laser-assisted bonding or automated alignment systems, can help ensure precise positioning and minimize alignment errors.
Case Studies: Successful Efpi Sensor Bonding

To illustrate the effectiveness of Efpi Sensor Bonding, let's explore a few case studies where this technique has played a critical role in sensor manufacturing and performance:
Optical Fiber Sensors

In the field of optical fiber sensors, precise bonding of fiber ends to connectors or other components is essential. Efpi Sensor Bonding techniques, such as epoxy bonding with controlled curing conditions, have been successfully employed to achieve reliable and stable connections, ensuring accurate optical measurements.
Infrared Sensors

Infrared sensors often require the bonding of prisms or lenses to the sensor housing. UV-curing resins have proven effective in these applications, providing rapid bonding and high-quality optical performance.
Pressure Sensors

Pressure sensors, used in various industries, often involve the bonding of diaphragms or other sensitive components. By utilizing advanced adhesives and precise bonding techniques, Efpi Sensor Bonding has enabled the production of highly accurate and durable pressure sensors, meeting the demanding requirements of industrial applications.
The Future of Efpi Sensor Bonding

As technology advances, the field of Efpi Sensor Bonding continues to evolve. Researchers and manufacturers are exploring new adhesives, bonding techniques, and automation processes to enhance the efficiency and reliability of sensor bonding. Here are some trends and developments to watch out for:
- Smart Adhesives: The development of smart adhesives with self-healing or self-sensing capabilities could revolutionize sensor bonding, offering enhanced performance and longevity.
- Nanotechnology: Nanoparticles and nanostructures are being explored for their potential in improving adhesive properties, such as strength, conductivity, and environmental resistance.
- Automated Bonding Systems: Automated bonding systems can improve efficiency, consistency, and precision in sensor bonding, reducing human error and increasing production rates.
- Eco-Friendly Adhesives: With growing environmental concerns, the demand for eco-friendly adhesives is on the rise. Researchers are working on developing sustainable adhesives that meet performance requirements without compromising the environment.
Conclusion

Efpi Sensor Bonding is a critical aspect of sensor manufacturing, ensuring the accuracy, stability, and longevity of measurement devices. By understanding the importance of proper bonding, choosing the right adhesives and techniques, and following best practices, manufacturers can produce high-quality sensors that meet the demands of various industries. As technology advances, the field of Efpi Sensor Bonding will continue to evolve, offering new opportunities for innovation and improved sensor performance.
What are the key factors to consider when selecting an adhesive for Efpi Sensor Bonding?
+When choosing an adhesive, consider factors such as the sensor’s intended application, environmental conditions, and desired bonding strength. Epoxy adhesives are versatile and offer excellent strength, while UV-curing resins provide rapid bonding. Anaerobic adhesives are suitable for metal-to-metal connections, and thermal bonding is ideal for plastic sensors.
How can I ensure proper alignment during Efpi Sensor Bonding?
+To ensure proper alignment, use precision alignment tools and techniques. This may include laser-assisted bonding or automated alignment systems. Maintaining consistent clamping pressure and following recommended curing conditions can also help achieve accurate alignment.
What are some common challenges in Efpi Sensor Bonding, and how can they be addressed?
+Challenges in Efpi Sensor Bonding include bonding to sensitive components, harsh environmental conditions, and achieving precise alignment. To address these challenges, choose adhesives and techniques suitable for the specific application, consider specialized adhesives with enhanced environmental resistance, and utilize advanced alignment systems or techniques.