The cost of batteries, particularly those used in electric vehicles (EVs) and energy storage systems, has been a significant factor influencing the adoption and scalability of these technologies. While the prices have been gradually decreasing over the years, batteries still remain a costly component, impacting the overall affordability and market penetration of EVs and renewable energy solutions. Understanding the reasons behind these high costs is crucial for developing effective cost-cutting strategies and accelerating the transition to a more sustainable and accessible energy landscape.
Factors Contributing to Battery Expenses
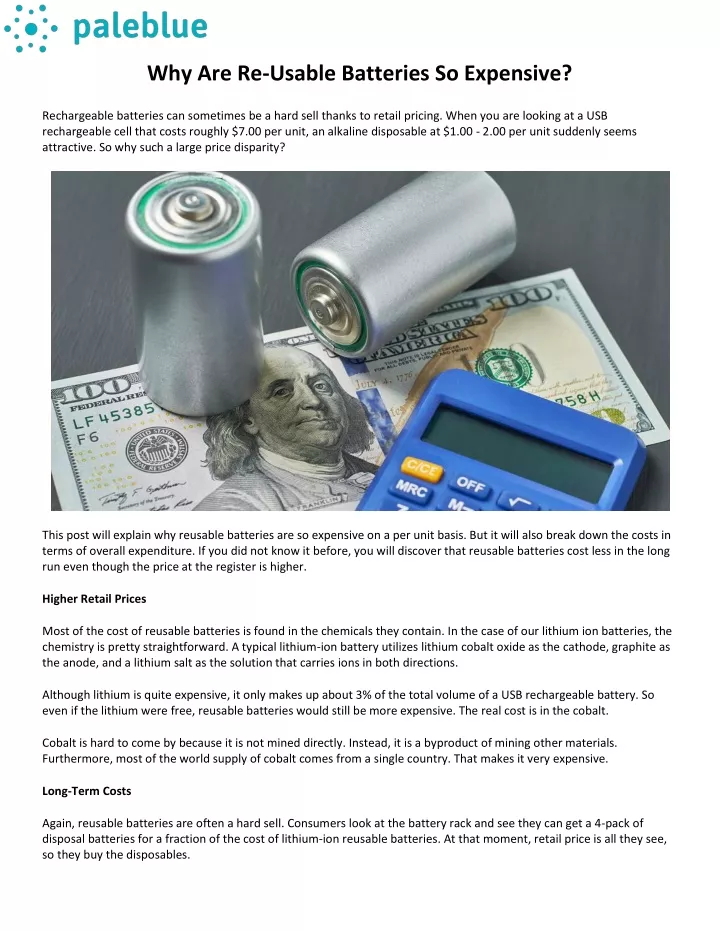
Several key factors contribute to the elevated costs associated with batteries, including:
- Raw Material Costs: The primary raw materials used in battery production, such as lithium, cobalt, nickel, and graphite, are finite resources with limited global supply. The mining and processing of these materials can be expensive and environmentally intensive, leading to high costs that are often passed on to consumers.
- Manufacturing Processes: The production of batteries is a complex and energy-intensive process, involving multiple stages of material preparation, cell assembly, and quality control. The need for specialized equipment, skilled labor, and stringent safety standards adds to the overall manufacturing costs.
- Research and Development: The battery industry is highly research-intensive, with ongoing efforts to improve performance, safety, and sustainability. Significant investments in R&D are necessary to develop new battery chemistries, optimize production processes, and enhance recycling technologies, all of which contribute to the overall cost structure.
- Scale and Infrastructure: The current battery manufacturing capacity is still relatively limited compared to the growing demand for EVs and energy storage systems. Building new manufacturing facilities and scaling up production requires substantial capital investments, which can take time to recoup and may impact the short-term affordability of batteries.
- Regulatory and Environmental Considerations: Ensuring compliance with environmental, health, and safety regulations adds to the cost of battery production. Additionally, the need for proper waste management and recycling infrastructure further increases the overall expenses associated with batteries.
Cost-Cutting Strategies for Battery Production
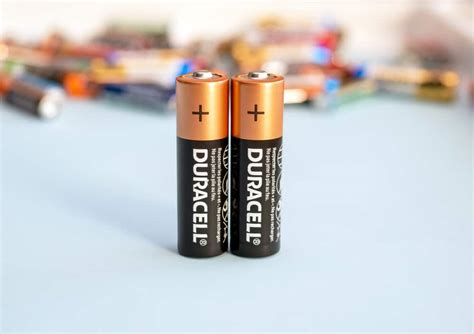
To address the high costs of batteries and promote their widespread adoption, several cost-cutting strategies can be implemented, including:
Optimizing Raw Material Sourcing
One of the most significant cost drivers in battery production is the acquisition of raw materials. Strategies to mitigate these costs include:
- Diversifying Supply Chains: Reducing reliance on a few key suppliers can help mitigate price volatility and supply chain disruptions. By diversifying the sourcing of raw materials, manufacturers can negotiate better prices and ensure a more stable supply.
- Developing New Battery Chemistries: Ongoing research into alternative battery chemistries that rely on more abundant and affordable materials can help reduce the overall cost of batteries. For example, lithium-iron-phosphate (LFP) batteries, which use iron instead of cobalt, offer a more cost-effective and environmentally friendly option.
- Recycling and Reuse: Implementing effective battery recycling programs can recover valuable raw materials, reducing the need for new mining operations. Additionally, reusing battery packs from retired EVs or energy storage systems can provide a cost-effective alternative to new battery production.
Enhancing Manufacturing Efficiency
Improving the efficiency of battery manufacturing processes can lead to significant cost savings. Some strategies to achieve this include:
- Automating Production: Investing in advanced automation technologies can reduce labor costs, improve precision, and increase production speeds. This not only enhances manufacturing efficiency but also improves overall product quality.
- Lean Manufacturing Techniques: Implementing lean manufacturing principles, such as just-in-time inventory management and process optimization, can minimize waste and reduce production costs. By streamlining operations, manufacturers can achieve significant cost savings without compromising quality.
- Collaborative Manufacturing Networks: Establishing collaborative relationships with other battery manufacturers or suppliers can help optimize production processes and reduce costs. By sharing resources, expertise, and best practices, manufacturers can achieve economies of scale and improve overall efficiency.
Advancing Research and Development
Continued investment in R&D is crucial for driving down the costs of battery production. Some key areas of focus include:
- Improving Battery Performance: Enhancing the energy density, cycle life, and charge/discharge rates of batteries can lead to more efficient and cost-effective energy storage solutions. By developing batteries with longer lifespans and higher energy capacities, manufacturers can reduce the overall cost per kWh.
- Developing New Manufacturing Technologies: Researching and implementing innovative manufacturing techniques, such as 3D printing or advanced coating technologies, can streamline production processes and reduce material waste. These advancements can lead to significant cost savings over time.
- Enhancing Recycling Technologies: Investing in research and development of more efficient and environmentally friendly recycling processes can help recover a higher percentage of valuable raw materials from retired batteries. This not only reduces the cost of raw material acquisition but also promotes a more sustainable battery lifecycle.
Promoting Market Growth and Competition
Encouraging market growth and fostering competition among battery manufacturers can drive down costs and improve accessibility. Some strategies to achieve this include:
- Government Incentives: Providing tax credits, subsidies, or other financial incentives for battery production and EV adoption can help stimulate market demand and attract new manufacturers. This increased competition can lead to more affordable battery solutions.
- Standardization and Interoperability: Developing industry-wide standards for battery chemistries, form factors, and charging protocols can simplify production processes and reduce costs. Standardization also enables easier battery swapping and replacement, improving overall system efficiency.
- International Collaboration: Facilitating collaboration between battery manufacturers, researchers, and policymakers from different countries can help share best practices, accelerate technology development, and promote the adoption of cost-effective battery solutions on a global scale.
Conclusion

The high costs associated with batteries present a significant challenge to the widespread adoption of electric vehicles and renewable energy systems. However, by implementing a combination of cost-cutting strategies, including optimizing raw material sourcing, enhancing manufacturing efficiency, advancing R&D, and promoting market growth and competition, it is possible to drive down battery costs and make these technologies more accessible and affordable. As the battery industry continues to evolve and innovate, these strategies will play a crucial role in shaping a more sustainable and equitable energy future.
How do battery costs compare to other energy storage technologies?
+While batteries are currently the most widely used energy storage technology, they are not always the most cost-effective solution. Alternative storage technologies, such as pumped hydro, compressed air energy storage (CAES), and flow batteries, can offer more competitive pricing for certain applications. However, batteries have the advantage of being more versatile, scalable, and suitable for a wider range of use cases, making them a critical component of the energy transition.
What role does government policy play in battery cost reduction?
+Government policies and incentives play a crucial role in driving down battery costs. Tax credits, subsidies, and other financial incentives can stimulate market demand for EVs and energy storage systems, leading to increased production volumes and economies of scale. Additionally, policies promoting research and development, infrastructure development, and battery recycling can further reduce costs and promote a more sustainable battery lifecycle.
How can consumers contribute to reducing battery costs?
+Consumers play a vital role in driving down battery costs by increasing market demand for EVs and energy storage systems. By adopting these technologies and supporting renewable energy initiatives, consumers can help create a more competitive market, leading to increased production volumes and cost reductions. Additionally, responsible battery disposal and recycling practices can ensure the recovery of valuable raw materials, reducing the need for new mining operations.